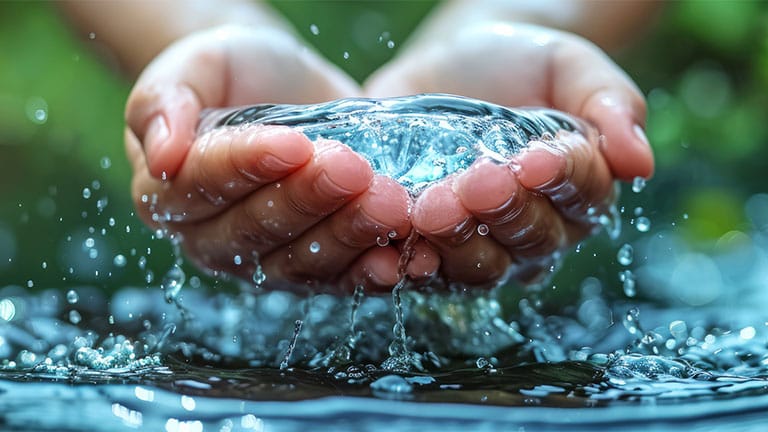
Sustainability
Our vision is to advance our environmental, social and governance practices consistent with our corporate values and inspire our industries through leadership and innovative products for a sustainable future.
Policies & Resources
These policies and procedures include the following: Anti-Bribery Policy, Conflicts of Interest Policy, Insider Trading Policy, Financial Code of Ethics, Whistleblower Procedure, CA Transparency in Supply Chains Act, Conflict Minerals Statement, Conflict Minerals Report, and Human Rights Statement.
Embracing Environmental Transparency
A. O. Smith Corporation embraces transparency by disclosing to CDP.
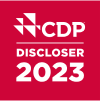